
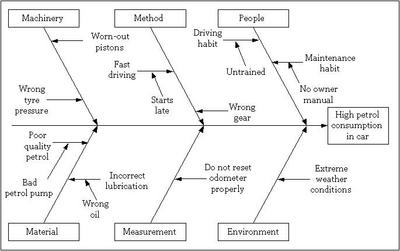
Machines: Any equipment, computers, tools, etc.Methods: How the process is performed and the specific requirements for doing it, such as policies, procedures, rules, regulations and laws.Man/People: Anyone involved with the process.The categories typically include: (Also see the 5Ms and 1P) Causes are usually grouped into major categories to identify these sources of variation. Each cause or reason for imperfection is a source of variation.Establish main causes and write down few main causes on the above horizontal line and few on below horizontal line and are placed on the tail of associated arrows.Step 3: Identify major causes contributing to the effect or a problem An effect may be positive like objective (to improve the process further) or negative like a problem (to identify customer dissatisfaction).Create an operational definition of a problem to ensure all the stakeholders will understand it.Identify and clearly write down the effect or a problem that needs to be analyzed.The diagram’s basic input is the brainstorming that pushes to identify all the possible causes rather than just more noticeable ones.įollowing are the steps to draw fishbone diagram Step 1: Identify the problem: The Cause and effect diagram is a structured graphical diagram to list all probable causes and also their relationship with the main effect or problem.
#Ishikawa diagram categories how to#
How to develop a Cause and Effect Diagram

This may be useful in a manufacturing environment as it includes material and machine categories. Here you may be able to identify critical supply chain disruptions, skills shortages, or process shortfalls.ĥM/1E Fishbone diagram: The categories in a 5M/1E Fishbone diagram stand for man, machine, method, material, measurement, and environment. This means that a project manager can exercise a great deal of flexibility in identifying factors specific to their particular project phases and environment.ĤS Fishbone diagram: The categories in a 4S Fishbone diagram are surroundings, suppliers, skills, and systems.

It also does not include pre-labeled categories. Simple Fishbone diagram: A Simple Fishbone diagram does not have as many branches as the others. Three common types of Fishbone diagrams are the Simple, 4S, and 5M/1E Fishbone diagrams. What works in a creative environment may not work in a manufacturing environment, for example. This is because projects can have major differences in processes, complexities, and more. There are a few different types of Fishbone diagrams. What are the different types of Fishbone project management diagrams?
